The HSE has released new guidelines in relation to PAT testing in relation to small electrical equipment.
The guide gives no clearer indication as to how often PAT tests should be undertaken and further advocates that ‘self checking and inspection’ maybe sufficient to maintain items between PAT tests. Employers should encourage employees to undertake their own ‘user checks’ from time to time.
User checks should be used to check for the following;- Lead and wire covering being damaged, frayed or cut- Plug cover and pins are not cracked, or bent- Checking for loose parts and screws overall- Check for signs or overheating.- If the item has previously been stored in an unsuitable place, or previously been subjected to unsuitable conditions if it is suitable to continue using.- Are there any hazards in the working proximity which would lead to it not correctly operating? – Checking cables are not trapped or knotted.- Is the selected equipment suitable for the job in hand? – Removal of the plug cover to check that there is no damage, signs of overheating, water damage. Also to check the wires are correctly placed and the correct fuse is being used.
Further the importance of reporting faulty equipment as soon as discovered is reiterated. Employers should make sure that all employees understand their responsibility in reporting such faults and how they should do so.
The Guide sets out what appliances are suitable for ‘user checks’.
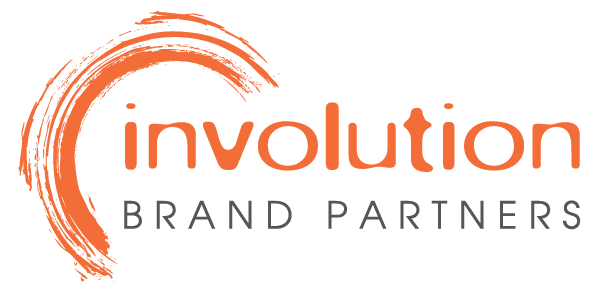
Leading experts in print, promotional clothing, staff uniforms, branded merchandise and PPE. Involution is your brand partner for promotional marketing and workwear, a one-stop-shop for your branded marketing needs for any business size and industry.
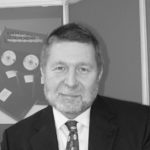