There are persistently high rates of fatal incidents and serious injuries and work-related ill health in the Motor Vehicle Repair (MVR). A typical Engineering Workshop may have a wide range of potentially dangerous plant, equipment and machinery in use; and equally there may be potentially dangerous places within the Workshops, such Spray Paint Booths / Rooms, or Vehicle Pits etc.
The HSE have produced guidance that is designed to help employers operating within the MVR sector and everyone working within the industry; to achieve good standards of health and safety and reduce injuries and ill health by identifying the hazards (something with the potential to cause harm, or damage to plant, property and equipment) and eliminating or controlling risks (the likelihood that harm will be realised coupled with the severity (or consequences) of harm when realised).
Guidance published by the HSE is often updated. Employers and the self-employed must keep pace with widely available guidance on health and safety related matters. This industry-specific guidance covers the management of health and safety, as well as outlining the specific risks associated with MVR work, giving practical advice to keep employees and others safe and how to maintain a healthy place of work. Much of this advice and guidance can be downloaded FOC from the website of the HSE and other interested bodies.
Five Steps to a Proper Risk Assessment in MVR
There are five essential steps to conducting a successful risk assessment for a business operating in MVR. These are laid out by the HSE and cover the following areas:
1. Identifying the hazards in your workplace
2. Finding out which workers are at risk of harm, and identifying how this might occur
3. Assessing the risks and thinking about the best precautions that can be taken so as to minimise the degree of risk of harm present in each situation
4. Making good use of the results of the risk assessment every day to ensure people are kept safe from harm
5. Ensuring there are regular checks; so that the employer can see that the measures taken are still working. Employers must review their Risk Assessments on a regular basis; although the frequency of such reviews is not prescribed.
These five steps should ensure your workers are able to make the most of a much safer workplace.
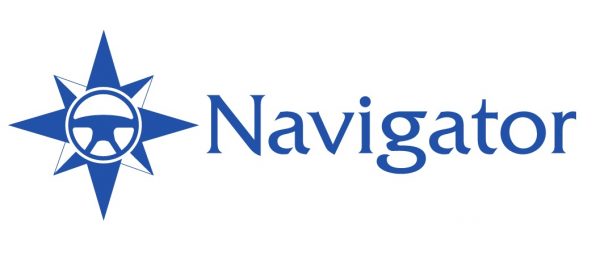
Our dealers use us to help them be more Efficient and Profitable!
You can use our Dealer and Lead Management software to integrate all dealership departments, both online and physical ; providing all in-house functions; Invoicing, Stock Management, Accounting and Marketing as well as interfacing for advertising, ecommerce and more.
Step 1 – Identifying Hazards in the Work Place
A hazard can be described as being anything with the potential to cause harm to persons, or damage to plant, property and equipment. Risk can be defined as being the likelihood that harm will occur coupled with its severity or the outcome of harm, i.e. from a minor injury through to fatal injury; or minor damage through to catastrophic or irreparable damage.
A good risk assessment is not about creating huge amounts of paperwork. An effective risk assessment process is more about identifying the hazards and then selecting sensible measures to control the risks to the health and safety to persons in the workplace.
Employers will therefore need to think about how accidents and ill health could happen in their workplace and then concentrate their efforts on real risks – those that are most likely to be realised and which will cause the most harm to persons when exposed to the hazard.
One of the most important aspects of an employer’s risk assessment is the need to accurately identify the potential hazards in the workplace. A good starting point for any employer is to firstly walk around the place of work and properly consider any hazards associated with the work done; or within the work environment itself. In other words, what is it about the work activities, processes or substances used; or the workplace itself that could cause injury to employees, or could harm employee health?
The following will help the employer to identify the hazards that are probably going to matter:
· Check manufacturers’ instructions or Material Safety Data Sheet (MSDS) for work equipment and chemicals or products that are used. These documents can be very helpful in explaining the hazards and putting each in to proper perspective.
· Look back at accident and ill-health records – examining the Accident Book and other records that are associated with previous accidents / incidents can often help employers to identify the less obvious hazards.
· Take account of non-routine operations (e.g. maintenance, cleaning operations or changes in production cycles; i.e. changing the paint used for paint spraying operations) when going through the workplace activities to ensure the completed Risk Assessment is suitable and sufficient.
· Remember to think about long-term hazards to health (e.g. high levels of noise or exposure to harmful substances). Occupational ill-health is by far the greater reason for absence from work of employees when compared with injuries at work. Employers should be looking to reduce all reasons for absence from work; be it occupational ill-health; or injury at work. The risk assessment process will contribute towards this aim.
· Visit the HSE website – HSE publishes practical guidance on hazards and provide possible risk control measures for the employer to consider.
There are some hazards with a well recognised risk of harm to persons; for example, working at height, working with chemicals, working with machinery and exposure to harmful dusts; such as asbestos fibres. Depending on the type of work that the employer undertakes as part of their business there may be other risks that are relevant to motor vehicle repair and maintenance.
Step 2 – Deciding Who Might Be Harmed
The employer must then think how employees (or others who may be present, such as contractors or visitors) might be harmed. Employers should ask their employees what they think are the hazards that they are faced with – employees may notice things that are not obvious to the employer and they may have some good ideas on how to control the risks.
Employers will need to be clear about each hazard and clear about who might be harmed. This approach (working with employees) will often help employers to then identify the best way of controlling the risk. This approach does not mean listing everyone by name, but rather identifying groups of people (e.g. people working in the storeroom or those in the vehicle workshop, or those in the Car Showroom).
Employers should take account of the following:
· Some workers may have particular requirements, e.g. new and young workers, migrant workers, new or expectant mothers, people with disabilities, temporary workers, contractors, homeworkers and lone workers (visit www.hse.gov.uk/ toolbox/workers).
· Think about those persons who might not be in the workplace all the time, such as visitors, contractors and maintenance workers.
· Members of the public; especially if they could be harmed by the work activities undertaken.
· If the workplace is shared with another business, then each employer (sharing a place of work) should consider how their work affects other (non-employees) and how other employers work activities may affect the health and safety of their own employees. Employers will need to talk to each other and make sure that adequate controls are identified and put into place.
· Ask workers if there is anyone that may have been missed.
Step 3 – Evaluating the Level of Risk to Persons
Having identified the hazards employers must then have to decide how likely it is that harm will occur; i.e. the level of risk and what to do about it. Risk is a part of everyday life and employers are not expected to eliminate all risks. What the employer must do is make sure they know about the main risks to the health and safety of persons and the measures needed to manage risks responsibly.
Generally, employers are required to do everything that is ‘reasonably practicable’ to protect people from harm. Employers do not need to take action if such action would be grossly disproportionate to the level of risk.
The employers risk assessment should only include what they could reasonably be expected to know – employers are not expected to anticipate unforeseeable risks.
Employers should look at what they are already doing to manage risk; including the risk control measures already have in place. Employers should ask themselves; “Can I get rid of the hazard altogether – and if not, how can I control the risks so that harm is unlikely?”.
Some practical steps that employers could take include:
· Trying a less risky option;
· Preventing access to the hazards;
· Organising the work to reduce exposure to the hazard;
· Issuing protective equipment;
· Providing welfare facilities such as first aid and washing facilities;
· Involving and consulting with workers.
Improving health and safety in the workplace need not be cost-prohibitive; for instance, placing a mirror on a blind corner to help prevent vehicle accidents is a low-cost precaution, considering the consequences if it goes wrong. Very often a failure to take simple precautions can cost an employer a lot more if an accident at work does happen!
Employers should involve their workers in identifying risk control measures so as to ensure that their proposals will work in practice and won’t introduce any new hazards.
Those employers that control a number of similar workplaces containing similar work activities can produce a model risk assessments reflecting the common hazards and risks associated with these activities.
Employers may also have access to model risk assessments developed by others, such as Trade Associations, employers’ bodies or other organisations concerned with a particular work activity. Employers may decide to apply these model assessments at each workplace; this should only be done if the employer can:
· be satisfied that the model risk assessment is appropriate to their type of work; and
· the model can be adapted to the detail of their own work situations, including any extension necessary to cover hazards and risks not referred to in the model.
Step 4 – Record the significant findings of the Risk Assessment
Employers will need to make a record of their significant findings – the hazards, how people might be harmed by them and what they have in place to control the risks. Any record produced should be simple and focused on the specified risk control measures.
If an employer has fewer than five employees, then they do not need to write anything down. However smaller employers may find it is useful to maintain written records so that they can review assessment at a later date, for example if something changes.
Where the employer does have five or more employees they will be required by law to set down in writing the risk assessment.
Any paperwork produced as part of the risk assessment process should help the employer to effectively communicate and manage the risks within the business. Employees will need to be informed about the hazards that they may face whilst at work and told about the steps taken by their employer to reduce the risk of harm. For most people this does not need to be a big exercise – just note the main points down about the significant risks and what you concluded – and thoroughly brief those employees affected.
When writing down the results of the risk assessment keep it simple, for example ‘Fume from welding – Local Exhaust Ventilation (LEV) is used and it is regularly checked and serviced’.
Any risk assessment undertaken so as to comply with regulation 3 to the MHSWR’99 must be suitable and sufficient, i.e. it should show that:
· A proper check was made;
· You asked who might be affected;
· You dealt with all the obvious significant hazards, taking into account the number of people who could be involved;
· The precautions are reasonable, and the remaining risk is low;
· You involved your employees or their representatives in the process.
Where the nature of the work changes fairly frequently or the workplace changes and develops, or where workers move from site to site, the employers risk assessment may have to concentrate more on a broad range of risks that can be reasonably anticipated.
If the employers risk assessment identifies a number of hazards, then there may be a need to put each in an order of importance and address the most serious risks first – this called prioritising risk.
Identify long-term solutions for the risks with the biggest consequences, as well as those risks most likely to cause accidents or ill health. Employers should also establish whether there are improvements that can be implemented quickly, even temporarily, until more reliable controls can be put in place.
Remember, the greater the hazard the more robust and reliable the measures to control the risk of an injury occurring will need to be.
Step 5 – Review Risk Assessments
Employers must make sure their risk assessment stays up to date. Few workplaces stay the same. Sooner or later employers will bring in new equipment, or new substances or introduce new processes and procedures that could lead to new hazards. It makes good sense therefore to review what is being done as part of an ongoing basis. Employers should look at their risk assessment on a regular basis (regular is not specified in law; but every 12 months is usually seen as being appropriate) and during this review process they should ask:
· Have there been any significant changes since the last assessment?
· Are there planned improvements that still need to be made?
· Have any employees reported a problem since the last risk assessment?
· Has the business learnt anything from past accidents or near misses that have occurred?
In summary there are 5 essential steps to conducting a successful risk assessment for those operating in motor vehicle repair. These are laid out by the HSE and cover the following areas:
1. Identifying the hazards inherent in your workplace;
2. Finding out which workers are at risk of harm, and identifying how this might occur;
3. Assessing the risks and thinking about the best precautions you (and they) can take to minimise the degree of risk present in each situation;
4. Making good use of the results of the risk assessment every day to ensure people are kept as safe as is practicably possible;
5. Ensure there are regular checks so you can see the measures taken are still working; also you must review the risk assessment on a regular basis.
Using Chemical Products in MVR Safely
Risk Assessments should be performed before using any chemical product. You may need expert help. People and the environment can be harmed through improper use products used by the MVR industry.
• Always read and understand the instructions on the label and in any leaflet supplied with the product. Failure to follow these instructions may be an offence and could lead to prosecution.
• Follow the advice in the statutory Approved Code of Practice in the COSHH Regulations and the Manufacturers / Suppliers publications when using chemical products. it reveals how to store,
handle, use and dispose of chemical and products and the associated waste properly.
• Make sure your employees use any Personal Protective Equipment identified in these instructions.
• Do not eat, drink or smoke when working with chemical products.
• Wash off splashes from the skin and clothing immediately, and wash before eating, drinking, smoking or taking a rest break.
• Do not use faulty application equipment.
• Do not overfill containers and secure all caps and lids before use.
• Keep a record of all chemical products used.
Preventing Accidents that Lead to Injury and Ill-Health
A large number of incidents are caused by the same basic health and safety mistakes that have been injuring and killing people for decades. Here are just a few key areas that the HSE have identified as being causes of occupational accidents leading injury and ill-health.
• Working from ladders – Almost a 20% of reportable falls from height in the workplace caused when working from ladders. Whether it is a poorly maintained ladder, or incorrect use, or simply a ladder that is not fit for purpose, it’s an issue HSE Inspectors come across frequently;
• Working at height – One in every 12 recordable injuries in Britain’s workplaces is a result of a fall. Falls account for around 700,000 lost working days annually. HSE Inspectors repeatedly see people working on roofs or scaffolding without appropriate safeguards.
• Workplace transport – Vehicle-related incidents are a major cause of concern, accounting for about around 50 deaths and more than 1,500 injuries annually. Ensure your employees follow rules such as keeping vehicles and people apart and make sure loads are properly secured when being moved.
• Machinery safety guards – There are around a dozen deaths and 40,000 injuries each year due to incidents where workers have been using machines, and most of these are easily prevented. HSE Inspectors often witness the aftermath of horrific incidents caused by poorly maintained machinery; particularly those with dangerous moving parts.
• Unhygienic or non-existent welfare facilities – HSE Inspectors have exposed some filthy and inadequate workplace bathrooms and kitchen areas. Poor sanitation and cleanliness can be a breeding ground for all types of diseases. Workers should have access to clean toilets, wash basins, drinking water and a means to heat food.
REMEMBER: Every workplace is full of potential hazards. There are many hazards that could be said to be particular to the agricultural industry, but no matter what your workplace consists of or where it is, you will be presented with a range of potential hazards on a daily basis.
How Can You Minimise the Hazards Present in the Workplace?
Being alert to the hazards around you is the first step. Some hazards will be more obvious than others. For example, a spillage presents a tripping or slipping hazard. Coiled wires or cables can also be tripped over.
But there are many other potential dangers. If you have one or more machines that your employees use on a regular; or even an occasional basis, there is the possibility of electrocution or injury. The more alert and aware you are to risks to worker safety and health then the easier it will be to stay safe and healthy and minimise the risks to your employees and others.
Awareness of the Health and Safety Legislation
Every workplace must adhere to the requirements of the Health and Safety at Work Act 1974. It is wise to read this so you are fully aware of all of your duties under the Act and of additional rules that apply in MVR. The Act is divided into sections, but it is a good idea to read through thoroughly and then pick out the specific areas that apply to you as an employer and to your business. This will ensure you are following all the required Health and Safety rules and regulations relevant to your business.
The UK law states that all work equipment (machinery included) must be suitable for the task. It should be properly maintained, stable and with dangerous parts safeguarded. Proper training and information should also be available for each item. Stop controls – including emergency stops – should also be included.
Staying Safe When Working with Machinery Used in MVR
The machinery typically used in the MVR sector can cause of many serious accidents that result in injury; and sometimes life-changing injury. There are many reasons for this, including unsuitable use of machinery. There are also many cases where safety guards have been left off or not provided at all.
Using Tools, Machines and Plant and Work Equipment Safely
Any tools, machines and plant and work equipment provided and used must always be suitable for the intended purpose. Make sure you are able to recognise dangerous parts and assess how you can prevent injury when performing your own risk assessment. If you provide safeguards that are inconvenient to the user; or those that can be easily be removed, you could be encouraging your employees to break the law, and to risk serious injury!
Implement a system to check that each machine is safe to use. Sometimes safety is dependent on how equipment is installed. Always inspect it to ensure it is correctly set up. Regular inspections for deterioration should also be done. Keep records of these inspections.
All workers – including you – should use machines according to the instructions they were supplied with. All guards should be in position and suitable for the job. Proper maintenance is essential to keep the machines in good order. Safety checks should be performed before each use, so any defects can be spotted and fixed.
Controls should be clearly marked to illustrate their purpose and which machine they relate to. You shouldn’t be able to operate these controls by unintentionally. Proper lighting should be provided for stationary machines. Electrical machinery should be isolated and locked off if safety guards or other safety devices are removed. Everyone should be trained to work safety and have the required protective clothing and protective equipment.
Check that safeguards are fitted. They should be strong and securely attached to the machine. They should also be self-locking and require a tool to open them. Safeguards should be made from a strong material (plastic is easy to damage) and should always be checked and maintained.
If guards are interlocked, check the machine can’t start before the guard is in position. Also check that opening the guard will stop the machine or that part. For example, the interlocking valve or switch (where fitted to a machine) should be robust for the job and be difficult to defeat.